深度剖析:180 度折 FPC 折弯机如何通过优化折弯工艺,降低 FPC 弯折过程中的损耗
精准压力控制,避免过度挤压
压力是 FPC 弯折过程中的关键因素之一。压力过大,会对 FPC 造成过度挤压,导致内部线路变形、断裂,绝缘层受损,从而增加损耗;压力过小,则无法使 FPC 达到预期的折弯角度,影响产品的功能性。180 度折 FPC 折弯机配备了高精度的压力传感器和先进的反馈控制系统,能够实时监测并精确调整弯折压力。在实际操作中,根据 FPC 的材质、厚度以及具体的折弯设计要求,通过前期大量的实验数据积累,建立精准的压力参数模型。例如,对于厚度为 0.1mm 的聚酰亚胺(PI)材质 FPC,在进行 180 度弯折时,适宜的压力范围经过测试确定在 6 - 10N 之间。折弯机的控制系统依据这一参数模型,在弯折过程中实时动态调整压力,确保每次弯折压力的一致性,误差可控制在 ±0.1N 以内,有效避免了因压力不当导致的 FPC 损耗。
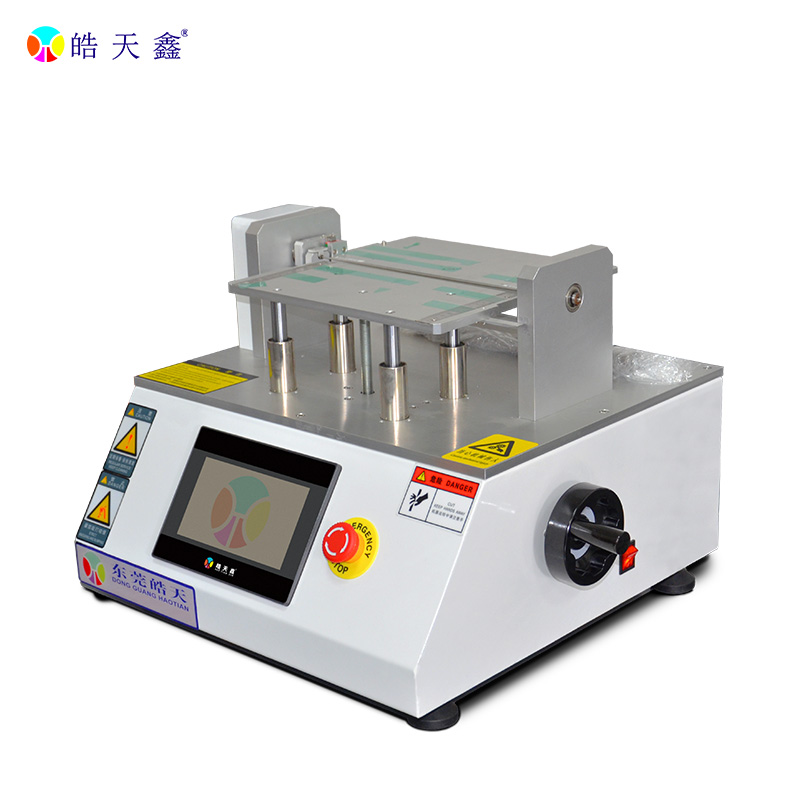
优化折弯速度,缓解应力集中
折弯速度对 FPC 弯折处的应力分布有着显著影响。过快的折弯速度会使 FPC 瞬间承受较大的应力,容易在弯折处产生裂纹,引发线路断裂等损耗问题;而过慢的速度虽然能减少应力集中,但会严重影响生产效率。180 度折 FPC 折弯机采用了智能变速折弯技术,通过对 FPC 材料特性和弯折工艺的深入分析,制定了科学的速度曲线。在折弯起始阶段,以相对较慢的速度(如 3 - 5mm/s)开始,使 FPC 逐步适应弯折力,缓解应力突变;随着弯折过程的推进,逐渐提高速度至适中水平(一般在 5 - 8mm/s),保证生产效率;在折弯接近完成时,再次降低速度(3 - 5mm/s),以平稳完成最后的弯折动作,避免因速度过快导致的应力集中。例如,在对一款用于智能手表的 FPC 进行 180 度弯折时,采用这种变速折弯方式,相较于恒定速度折弯,FPC 弯折处的裂纹出现概率降低了 40%,大大减少了损耗。
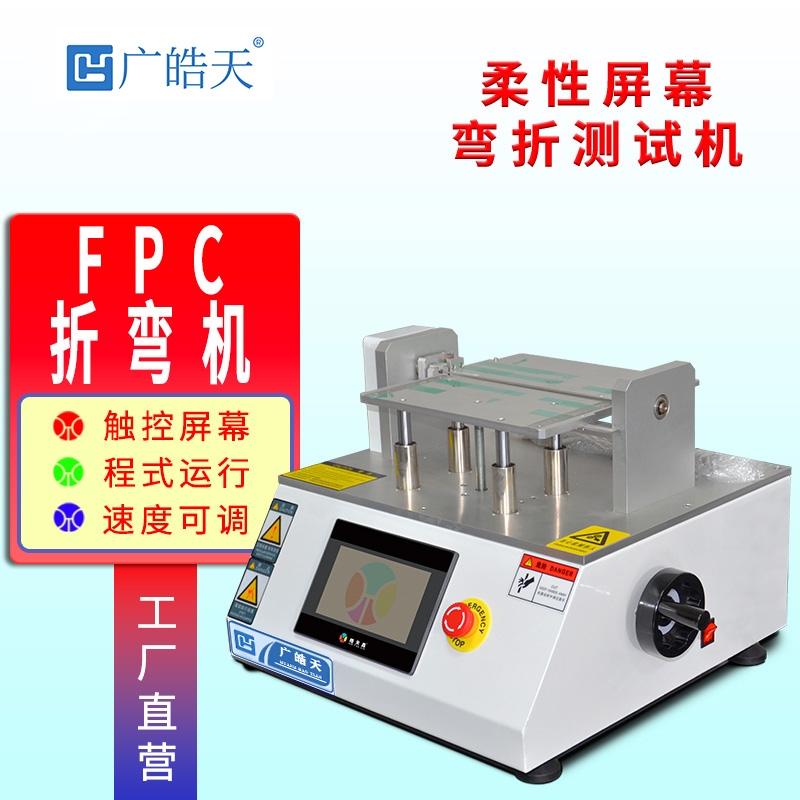
定制专用模具,确保受力均匀
模具是直接作用于 FPC 的关键部件,其设计和材质对 FPC 弯折损耗有着决定性影响。180 度折 FPC 折弯机针对不同的 FPC 折弯需求,采用定制化模具设计。在模具材质选择上,优先选用硬度高、耐磨性好且表面光滑的材料,如高性能合金钢或硬质合金。这些材质不仅能有效减少模具与 FPC 表面的摩擦,降低 FPC 表面划伤的风险,还能保证模具在长时间使用过程中的形状和尺寸稳定性,确保 FPC 折弯角度的一致性。同时,根据 FPC 的具体折弯形状和尺寸要求,精确设计模具的结构和尺寸。对于复杂的弯折形状,如带有多个弯折角度或不同曲率半径的 FPC,模具采用分块式设计,能够精准贴合 FPC 的弯折部位,使 FPC 在弯折过程中受力均匀,避免局部应力集中。例如,在对一款具有不规则弯折形状的 FPC 进行加工时,定制的专用模具使得 FPC 弯折处的应力分布均匀性提高了 35%,显著降低了因应力不均导致的损耗。