数据波动大:冷热温控试验箱的均温性改进技术路径
维风道优化技术,实现气流均匀覆盖
传统试验箱因风道设计不合理,易出现气流死角,导致温度不均。我们研发的三维立体循环风道系统,采用 CFD(计算流体力学)仿真技术进行设计优化。风道在箱体顶部、侧面及底部均设有精密风口,形成水平与垂直双向送风模式。运行时,高性能离心风机以 5m/s 的风速驱动气流高速循环,配合特殊扰流叶片结构的涡轮式搅拌器,将冷热气流充分打散并均匀分布至箱内每个角落。经实测,该技术使箱内温度均匀性提升 60%,有效消除温度分层现象,确保每个测试样品都能处于一致的温度环境中。
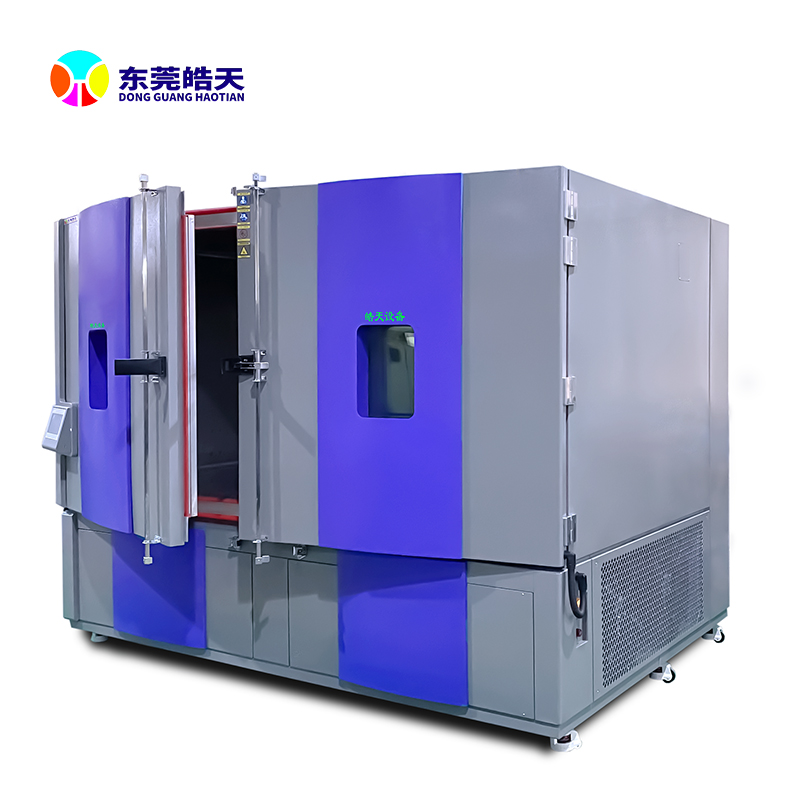
智能多区温控系统,精准调节温度偏差
试验箱内置 16 组高精度铂电阻温度传感器矩阵,实时采集箱内各区域温度数据,精度可达 ±0.1℃。基于 AI 神经网络算法的智能控制系统,可对每个传感器数据进行毫秒级分析处理。当检测到区域温度偏差时,系统自动调整对应区域的加热、制冷模块功率,实现独立补偿调节。即使在 - 70℃至 200℃的宽温域冲击下,也能将任意两点间的温差严格控制在 ±0.5℃以内,解决传统单点控温导致的数据波动问题,为高精度测试提供可靠保障。
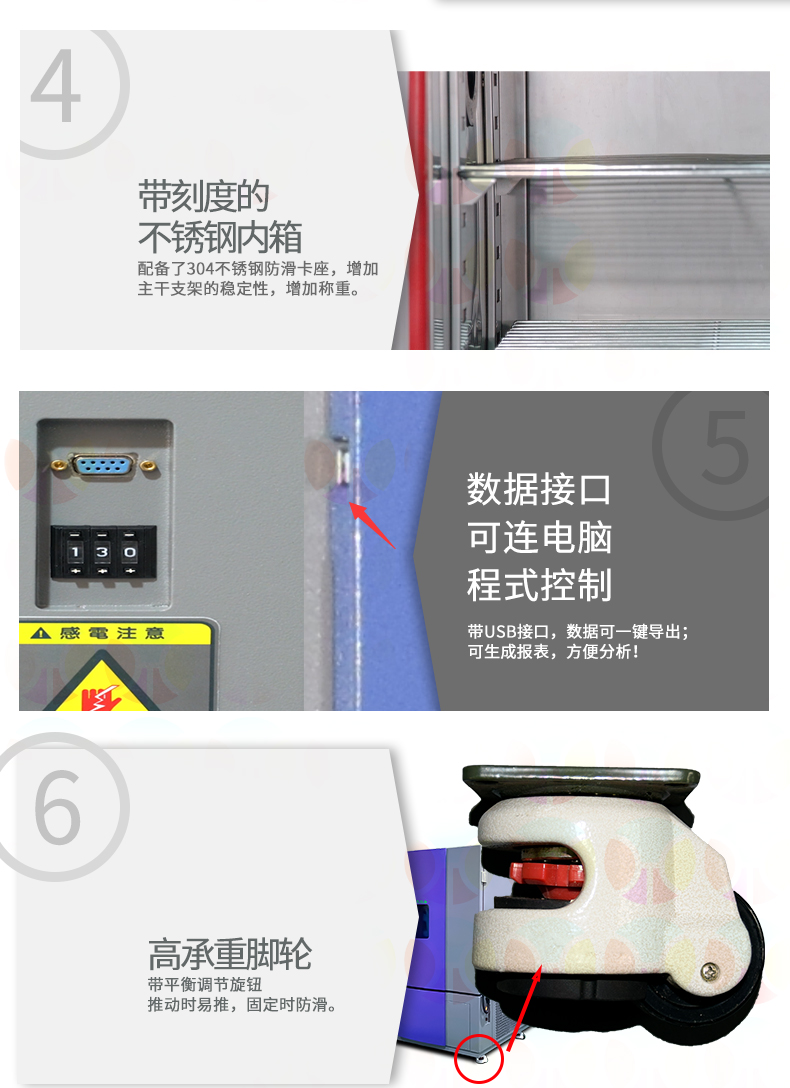
双层隔热匀温结构,减少边缘温度衰减
箱体采用双层中空隔板设计,中间填充高效真空绝热材料,导热系数仅为 0.002W/(m・K),有效阻断箱体边缘与外界的热交换。同时,内置环形加热丝与制冷管路,形成立体匀温层。经第三方检测,设备边缘区域与中心区域温差仅为 ±0.2℃,相比传统试验箱降低 80%,消除了边缘温度衰减现象,实现全空间温度均匀覆盖,确保测试结果真实反映产品性能。
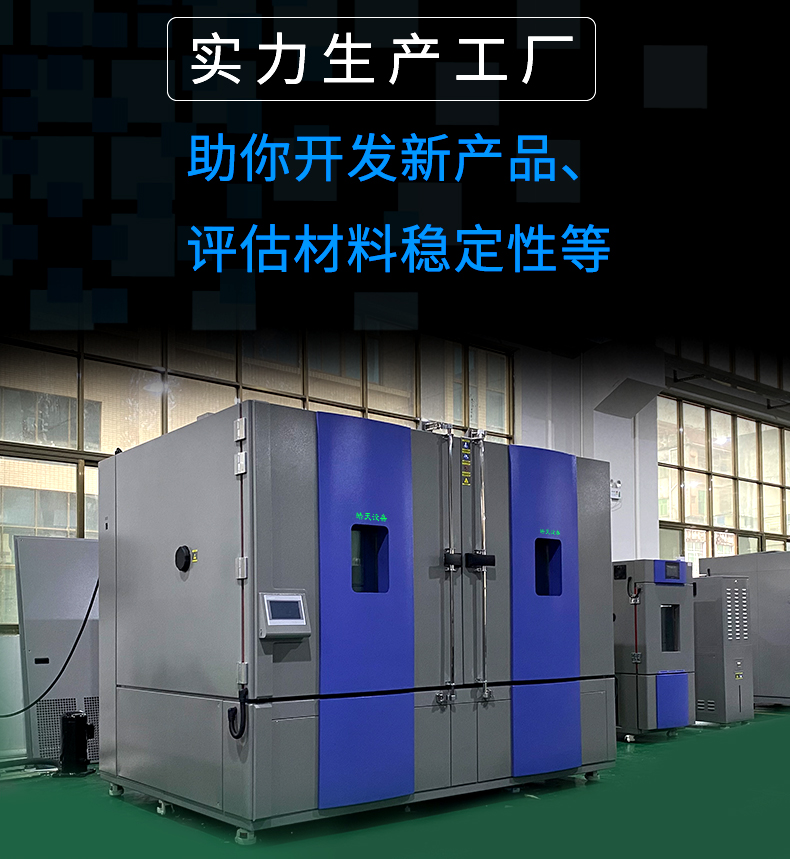
动态气流补偿技术,应对复杂测试工况
针对不同测试样品的尺寸、材质差异导致的气流扰动与热传导变化,我们开发了动态气流补偿技术。当系统检测到样品负载变化时,会自动调整风机转速、风道开合度以及冷热交换功率。在测试大型汽车零部件等高负载样品时,系统加大气流循环强度与制冷制热功率;测试精密电子元器件时,则精细调控制冷量,避免温度过冲。该技术使试验箱在复杂工况下仍能维持稳定的均温性,测试数据波动幅度降低 70%,大幅提升测试结果的重复性与可信度。